Better products, cheaper and faster

Modern economy requires companies and professionals to think, design and manufacture products faster, cheaper and better than direct competitors. This can become a nightmare for old-school production processes. Time and cost involved with optimal design and thorough testing can easily become prohibitive, and one often has to choose to sacrifice one aspect in favor of feasibility: i.e. a more expensive product or a slower delivery.
With the rise of computing power, software solutions previously available only to huge niche companies are becoming accessible also for smaller realities and even independent professionals. This new era offers great possibilities for innovative players wanting to leverage modern solutions to address long lasting, well known design and manufacturing challenges.
PhyMo is a modular technology able to accurately simulate and reproduce physical behavior of objects and processes. Built upon state of the art libraries, allows its users to test and study complex phenomena in a virtual environment, using only 3D models and user defined conditions. It can be adopted in early design phase to compare a huge number of alternatives in terms of performances, in order to select the best solution with no need of prototyping nor physical testing.
Applications
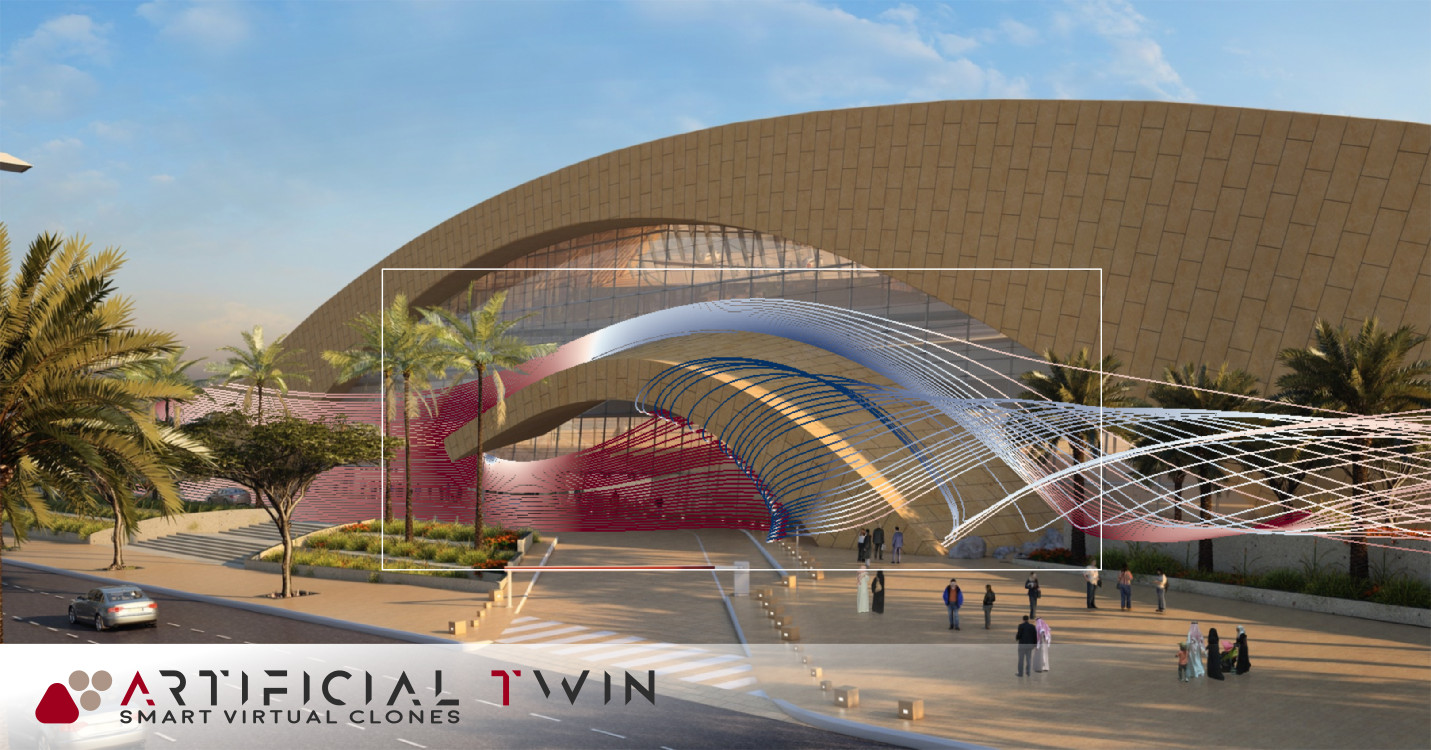
PhyMo can be adopted to investigate a very wide set of different contexts. Its flexibility and modularity plays a key role in allowing simulation and virtual reproduction of the most appropriate physical behavior, making it a state of the art product for a large number of fields. Some of the major possible applications are described in what follows.
External Aerodynamics / Hydrodynamics
Measuring aerodynamics/hydrodynamics performances of fluids interacting with object shapes, calculating quantities such as drag, lift/downforce and fluid dynamics induced moments is among the more typical fluid dynamics applications. PhyMo plays the role of a virtual wind tunnel where real scale tests are conducted on 3D models.
Internal Fluid Dynamics
Dealing with internal flows quantities like pressure drops, thermo-fluid dynamics variables trend, mass flow rates is common when optimizing design of valves, pipes, air vents. PhyMo reproduces real world physics allowing accurate and reliable insights.

Wind and Pollutant Dispersion
Often encountered in construction engineering, one may need to replicate the action of wind over buildings and simulate the dispersion of a non-reacting substance inside a modeled scenario. Using PhyMo it is possible to quantify wind-induced pressure loads, create pedestrian comfort maps, investigate urban heat island effect and determine pollutant diffusion paths.
Flows Interacting with Solid Particles
In same contexts, especially in the Oil & Gas sector, one may aim to reproduce phenomena involving complex interaction between fluids and solid particles, coupling their dynamics to obtain a high fidelity model. With this PhyMo module, one can conduct virtual experiments estimating variable trends and distribution, as well as complex processes like material erosion induced by solid particles impacts.
Multiphase and Rotating Flows
Even advanced scenarios, like behavior of non-reacting, non-miscible flows involving more than a single fluid phase (i.e. air/water) and flows interacting with rotating machinery (i.e. fans) can be simulated. In this configuration, PhyMo makes it possible to visualize and study contexts like tank filling, fuel sloshing, nozzle jet distribution, turbine blade shape or turbo-pumps efficiency optimization.

Stress and Deformation Analysis
Very common tests on 3D models of real products investigate their structural response: application of loads and constraints to examine stress distribution and visualize material deformation. PhyMo can easily be adopted to optimize product shape for best stiffness and lowest mass, as well as validate prototypes in the early development stages comparing different shapes or materials.
Modal Frequencies and Shapes
Another structural related analysis involves estimation of the frequency response using only virtual models and material information. PhyMo allows to obtain an user-defined set of natural frequencies of a 3D model and their correspondent modal shapes, providing the possibility to avoid resonance issues and to investigate noise generation/amplification.
Discrete Element Models
When dealing with fine grained particles materials, investigating their full-scale dynamics is of major interest. PhyMo is able to accurately model and reproduce particle-to-particle interaction making the user able to simulate and analyze product and processes like cyclones separators, screw conveyors and rotating mills.
Time-domain and Physics

All above applications can be characterized by a specific behavior in both the time domain and the physics involved. These aspects are particularly relevant when selecting the appropriate simulation method and configuration. Below, some examples and details are provided, showing the wide range of conditions PhyMo can cover.
Stationary or Transient / Static or Dynamic
Behavior in the time domain distinguishes between stationary / static phenomena and transient / dynamic ones, where alternative terminology refers to typical Computational Fluid Dynamics / Finite Element Analysis simulations respectively. PhyMo allows to address both these contexts. The user is able to investigate flow fields where there is no time evolution or material stresses and deformations resulting from a static load-constraint condition as well as time-dependent dynamics, like non-stationary fluid motion or impact structural analysis.
Laminar or Turbulent / Elastic or Plastic
Depending on the material physics involved in the simulation, different models need to be used: laminar or turbulent regimes (RANS | LES) and Newtonian or Non-Newtonian fluids for Computational Fluid Dynamics; Elastic, Plastic, Viscoplastic or Hyperelastic materials for Finite Element Analysis. PhyMo covers all these different conditions, providing modules to simulate all flow regimes and a very wide set of different fluids and materials, covering a huge number of different scenarios.