Understanding complex flow patterns
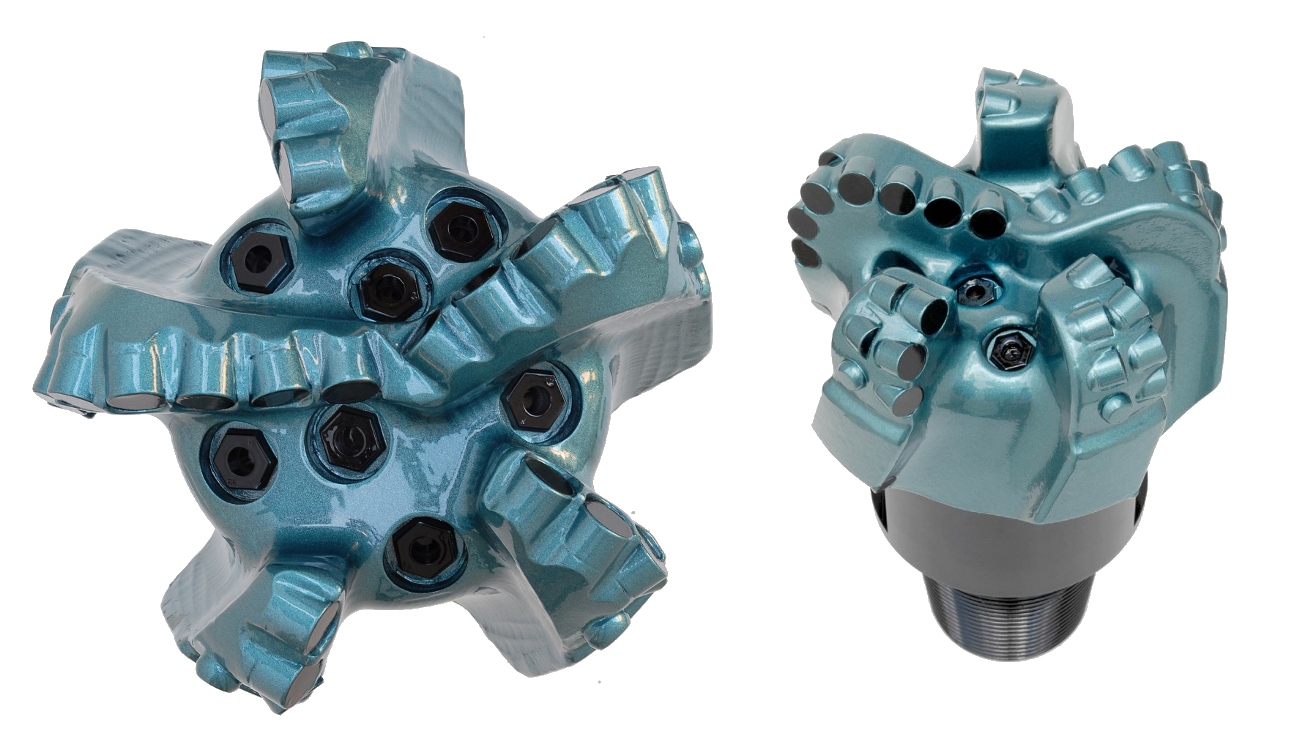
Drilling industry makes use of equipment that faces very harsh environments. In these contexts, optimal design choices are even more critical, if compared with other settings. They are responsible not only for guaranteeing proper equipment operating conditions, but they also have an impact on process performances, influencing for example drilling speed.
This project analyzes the flow around a drill bit like the one shown in the image on the right. It is composed by two fundamental components, the cutting elements and the fluid nozzles. One of the main function of the fluid injected through the nozzles is to remove pieces of rock generated by the cutting elements from the zone in front of it. In order to assure this is performed properly, many factors have to be considered: nozzles positioning, fluid injection velocity and cutting elements layout are the main ones.
Artificial Twin | PhyMo™ allows to perform virtual simulations by means of which the designer can obtain an accurate and meaningful insight on how the model under test will behave. In this specific case it has been used to evaluate flow configuration for a set of different models, allowing to compare them in terms of performances.
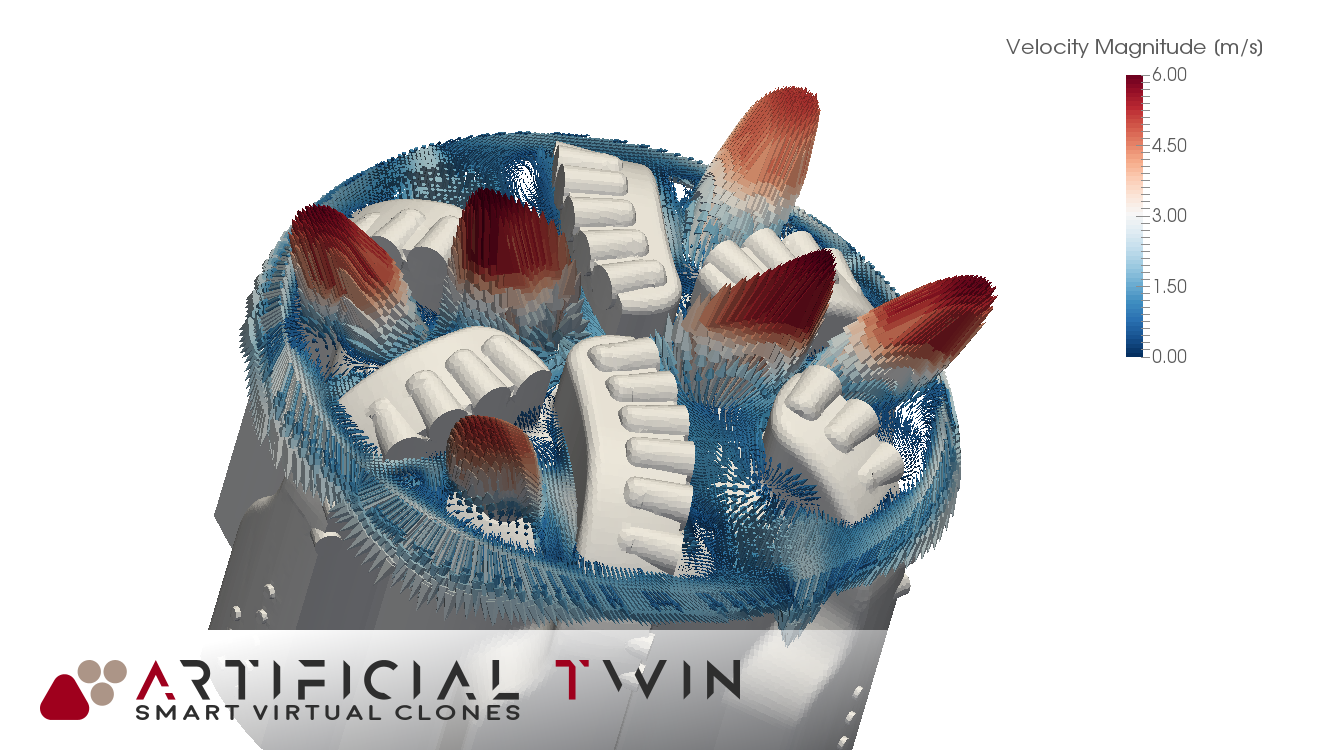
Analysis description
In order to conduct the analysis on a set of alternative designs, the first step is to produce a virtual 3D model for each object (CAD model). Many different formats can be used, usually a good choice is to rely on standard neutral formats such as STEP, IGES or STL.
Once the geometry is ready, the next step is to discretize the domain, creating the computational grid. This phase, called “Meshing”, must be performed carefully, since it strongly affects results quality and reliability. Our expertise in the field, together with Artificial Twin | PhyMo™ advanced meshing features, guarantees an high quality computational grid generation.
Finally, the last step is to assign the so called “Boundary Conditions”: these are conditions that uniquely define the problem, prescribing a variable value in selected zones of the domain. For example, in this case, the velocity of the fluid flow as been assigned at the inlet, the pressure has been assigned at the outlet and a no slip wall condition was selected for all physical surface. At this point the solver can be started: it will iteratively solve the equations governing the phenomena, gradually converging to a solution. The solution is then written to a solution file, used to evaluate performances and to compare different solutions.

Results visualization
The best way to understand simulation results is to visualize them by means of different techniques. In this page we reported three examples of typical visualization techniques that are very useful to understand what is happening inside the domain.
The first one, reported above, is a “Glyph vector plot”: it shows a distribution of arrows originating from a particular domain section, oriented accordingly to the velocity vector, with a length proportional to its magnitude and colored again accordingly to its magnitude.
The second example, shown on the rights, is a “Streamlines plot”: it shows trajectories of multiple fluid particles calculated integrating the local velocity vector, and colored by local velocity magnitude.
Finally, in the image below, is presented a “Contour plot” showing, for a user-selected section, a color map representing the local flow velocity magnitude distribution.
These are just few examples of a very huge set of post processing tools and procedures. Depending on the phenomenon of interest, one can choose the most suitable plot or chart for his case.

More advanced studies
The physics behind a drill bit in operation is fairly complex. In this study we dealt with a very relevant aspect: how the fluid flows around the cutting elements for a given inlet velocity. Flow lines and local velocity are fundamental elements to inspect how effectively cutting residuals are removed from the front portion of the equipment.
A more advanced inspection can be carried out by coupling flow dynamics with solid particle one, including generation of rock powder by the cutting elements. This complex phenomenon can be simulated with Artificial Twin | PhyMo™, and allows for a more accurate estimation of particles removal performance.
It should be clear the strategic advantage of using virtual simulation tools, especially in early design phases. One is able to compare different solutions without the need to realize and test real prototypes, resulting in a huge saving in terms of both money and time. These tools can be applied in a very wide set of contexts and industries, contact us to discover which possibilities are available for your specific case.